Технологии
3D печать
FDM - послойное наплавление
FDM (Fused Depsition Modelling) — технология трехмерной печати, при которой построение объекта идет за счет расплавления нити пластика, которая через экструдер подается на рабочую поверхность. Представляете себе процесс выдавливания крема для торта из кулинарного шприца? Если да, то вы легко поймете этот метод: “печатающая” головка выдавливает жидкий материал слой за слоем, перемещаясь свободно как в плоскости слоя, так и по вертикали. Материалом обычно служит катушка с пластиковой нитью. Через головку и специальное сопло нить подается на платформу, создавая твердое тело модели. Микропроцессор включает или выключает подачу материала, а также управляет движением головки в пространстве по трем координатам. Вдобавок, головка нагревает материал, чтобы материал был пластичным и как бы “вклеивался” в уже наплавленную субстанцию.

Как любой другой метод 3д печати, метод послойного наплавления начинается с подготовки компьютерной трехмерной модели. Программа загружает модель в формате stl и далее анализирует ее во всех сечениях и рассчитывает алгоритм наплавления. Кроме того, рассчитываются необходимые поддерживающие структуры. Эти элементы поддерживают отрицательные поверхности, арки и любые нависающие части фигуры.
После того, как модель напечатана, поддерживающие структуры удаляются. Для того, чтобы могли быть удалены, их обычно изготавливают из другого материала, который растворяется при погружении объекта в ванну со специальным раствором. Использование разных сортов материала для объекта и для поддержки необходимо для достижения высокого качества печати, что соответствующим образом сказывается на цене. Если нет особых требований к качеству продукции, и есть потребность уменьшить ее стоимость, иногда используют одинаковый материал.
FDM технологии используются промышленные термопластики, которые выдерживают высокие температуры и механические нагрузки. Однако чаще всего при данном методе 3d печати применяется ABS-пластик как наиболее надежный и универсальный материал, а также пластик PLA. Их температура плавления, с одной стороны, достаточно высока, чтобы избежать деформации под воздействием небольших температур в применяемых областях, но, с другой стороны, температура вполне достижима внутри печатающей головки.
SLA — лазерная стереолитография.
SLA — технология трехмерной печати, при которой жидкий фотополимер под действием светового излучения лазера меняет свои физические свойства и твердеет, образуя твердую поверхность в точке проекции лазера.
В емкость с жидким фотополимером помещается сетчатая платформа, на ней будет происходить выращивание прототипа. Изначально платформа находится на такой глубине, чтобы ее покрывал тончайший слой полимера толщиной от 0.025 до 0.1мм(клетка крови 0.01 мм) — это и есть приблизительная толщина слоя встереолитографии. Далее включается лазер, который воздействует на те участки полимера, которые соответствуют стенкам целевого объекта, вызывая их затвердевание. После этого вся платформа погружается чуть глубже, на величину, равную толщине слоя. Также в этот момент специальная щетка орошает участки, которые могли остаться сухими вследствие некоторого поверхностного натяжения жидкости.
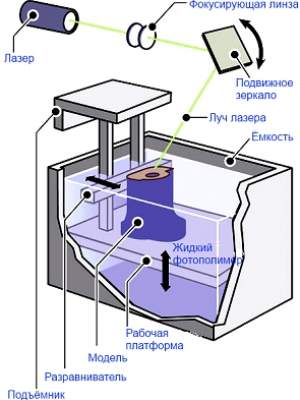
По завершению построения объект погружают в ванну со специальными составами для удаления излишков и очистки. И, наконец, финальное облучение для окончательного отвердевания. Как и многие другие методы 3D прототипирования,SLA требует возведения поддерживающих структур, которые вручную удаляются по завершении строительства.
Необходимо понимать, что из-за выборочного отвердевания накладываются жесткие двусторонние ограничения на компоненты и технологию процесса. Например, чем гуще смола изначально, тем легче её перевести в полимерное состояние, но и тем хуже её гидромеханические качества. Чем мощнее введенный в смолу фотоинициатор, тем меньшее время нужно слабому лазеру для засветки, но и тем меньшее время жизни у всего объёма смолы, так как он подвержен фоновой засветке. Именно золотая середина в технологии и компонентах является “ноу-хау” каждого производителя лазерных стереолитографов. Устройство и принцип действия таких машин у всех производителей идентичны, в любой SLA-машине возможно применение любого расходного материала после соответствующей настройки.
Одно из преимуществ 3D печати методом SLA — высокая точность прототипов, глакость поверхности и скорость. Большие объекты строятся в течения дня, хотя отдельные модели с особо сложной геометрией могут выращиваться до нескольких дней. Большинство SLA-машин работают с объектами размером примерно 50x50x60см, но есть и исключения.
Преимущества технологии SLA:
- Изготовление моделей любой сложности(тонкостенные детали, мелкая детали)
- Легкая обработка изготовленной детали
- Высокая точность построения и высокое качество поверхности
- Широта применяемых материалов, в том числе и выжигаемые модели
- Свойства применяемых полимеров позволяют использовать выращенный прототип в качестве готового изделия
- Низкий процент расходного материала на поддержку
- Низкий уровень шума стериолитографов
SHS - селективное тепловое спекание
Технология SHS (селективное тепловое спекание) – новая технология 3d печати на рынке 3D прототипирования. Впервые была представлена компанией BluePrinter ApS в 2011 году на выставке Euromold. Данная технология работает по следующему принципу: цифровую модель специальная CAD программа разрезает на множество слоев, после чего уже обработанную модель 3D принтер начинает печатать, насыпая порошок и спекая его термоголовкой слой за слоем .
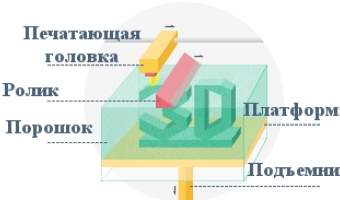
Технология SHS – это тепловое излучение, то есть – изменение физических свойств слоя термического порошка под воздействием термической головки. Казалось бы, что все достаточно просто и ясно, но к сожалению, потоком горячего воздуха трудно управлять. Поэтому прошло 2 года с момента анонсирования технологии до поступления 3d принтера Blueprinter в продажу. Преимущество технологии 3d печати SHS в том, что прототипы печатаются с высокой скоростью, а неиспользованный порошок можно пустить в работу повторно и помимо этого не требуется использовать вспомогательный материал для поддержки. Технология SHS применяется профессиональными инженерами, дизайнерами, архитекторами, конструкторами, и в образовательной сфере.
Основные преимущества технологии SHS:
- Минимальная толщина стенки составляет 1 мм;
- Возможность печатать объекты сложной геометрической формы с высокой детализацией;
- Оставшийся материал после печати можно использовать повторно;
3D Фрезеровка
ЧПУ фрезеровка
Фрезеровка ЧПУ начала применяться не так давно, ее прообразом можно считать используемую на обычных механических станках систему рычагов, которые соединяли шпиндель станка с шаблонной деталью. И только несколько лет спустя, управление фрезерным станком было поручено компьютеру, а для взаимодействия фрезеровщика-оператора со станком стали писать специальные программы. Обработка листового материала этим способом позволяет получить предметы большей точности, снизить количество брака, увеличить производительность, а также выпускать серийные детали со сложной геометрией поверхности в большом количестве. С помощью компьютера станку задается и скорость вращения шпинделя, и параметры его движения (глубина фрезеровки и линейные координаты). Современные станки позволяют выполнять 3D фрезеровку – это обработка заготовки несколькими фрезами одновременно в разных плоскостях. При этом предварительно на компьютере строится 3D-модель заготовки, «глядя» на которую станок воспроизводит ее с максимальной точностью.

На станках с ЧПУ выполняют сверление, рассверливание, зенке- рование, развертывание отверстий, нарезание в них резьбы. При сверлении заготовок используется целый набор различных циклов: простой, глубокое сверление, сверление с отскоком, повторяющееся сверление и т.д. Возможна комплексная сверлильно-расточная обработка заготовок различной конфигурации и степени точности.
На этапе построения траекторий движения инструмента можно проверить управляющую программу на возможные подрезы детали режущим инструментом, проконтролировать границы необработанных областей. Избежать подрезов позволяет использование сферических, торцевых и конических фрез. В ситуациях, когда технологу необходимо контролировать каждый шаг траектории инструмента, он может создавать траекторию инструмента по частям. На этапе врезания в заготовку в ряде случаев задают нижнюю границу обработки.
Современные САПР обеспечивают решение таких сложных задач, как оптимизация движений роботов, синхронизация их совместной работы, проверка возможности при их движении по траектории статических и динамических столкновений, оптимизация времен циклов. В конечном счете такие программы позволяют разрабатывать совершенные технологические линии.
Выбрав параметры режущих инструментов и рассчитав траекторию их перемещения, технолог может произвести моделирование на экране компьютера процесса обработки заготовки на станке с ЧПУ. Моделирование может иметь несколько режимов. В режиме анализа траектории отображается только передвижение инструмента без отслеживания изменения формы детали во время обработки.
В режиме моделирования обработки производится эмуляция обработки детали на станке с учетом снимаемого во время обработки припуска. Этот режим позволяет просмотреть зоны, где инструмент врезался в деталь, проанализировать наличие зарезов, визуально проконтролировать качество обработки. Зарезы образуются в местах обработки с отрицательным припуском.
Просмотр на экране монитора траектории движения инструмента на станке с ЧПУ и процесса обработки заготовки позволяет технологу оценить качество разработанных управляющих программ и в случае необходимости изменить их параметры.
Визуализатор обработки позволяет увидеть на компьютере, как будут выглядеть поверхности детали после обработки, выполнить анализ дефектов, показать распределение припуска между различными операциями, сократить цикл отладки управляющих программ. Предусмотрена возможность графического контроля состояния заготовки после каждого перемещения инструмента.
3D скаинрование
Белая структурированная подсветка
3D-сканеры, работающие по технологии структурированного света, представляют собой проекцию световой сетки непосредственно на объект, деформация этого рисунка и представляет собой модель сканируемого предмета. Сетка проецируется на объект с помощью жидкокристаллического проектора или другого постоянного источника света. Камера, расположенная чуть в стороне от проектора, фиксирует форму сети и вычисляет расстояние до каждой точки в поле зрения.

Идеальные карты также признаны полезными, как структурированные световые узоры, которые могут решить проблемы соответствия и позволяют не только обнаружить ошибки, но и исправить их. Преимущество 3D-сканеров, использующих структурированный свет, в их скорости и точности работы. Вместо сканирования одной точки в один момент времени, структурированные сканеры сканируют одновременно несколько точек или все поле зрения сразу. Сканирование всего поля зрения занимает долю секунды, а сгенерированные профили являются более точными, чем лазерные триангуляции. Это полностью решает проблему искажения данных, вызванного движением. Кроме того, некоторые существующие системы способны сканировать даже движущиеся объекты в режиме реального времени.
Сканеры, работающие в режиме реального времени, используют цифровую проекцию края и фазосдвигающую технику (одна из методик применения структурированного света), что позволяет захватить, восстановить и создать компьютерную модель с высокой плотностью деталей динамически изменяющихся объектов (к примеру, мимика) при 40 кадрах в секунду.
Лазерное сканирование
Триангуляционные лазерные 3D-сканеры относятся к активным сканерам, которые используют лазерный луч для того, чтобы прозондировать объект. Триангуляционные устройства посылают на объект сканирования лазер, а отдельная камера фиксирует расположение точки, куда попал лазер. В зависимости от того, как далеко лазер продвигается по поверхности, точка появляется в различных местах поля зрения камеры. Эта технология названа триангуляцией потому, что лазерная точка, камера и сам лазерный излучатель образуют своеобразный треугольник. Известна длина одной стороны этого треугольника – расстояние между камерой и лазерным излучателем. Также известен угол лазерного излучателя. А вот угол камеры можно определить по расположению лазерной точки в поле обзора камеры. Эти 3 показателя полностью определяют форму и размер треугольника и указывают на расположение угла лазерной точки. В большинстве случаев, чтобы ускорить процесс получения данных, вместо лазерной точки пользуются лазерной полосой.
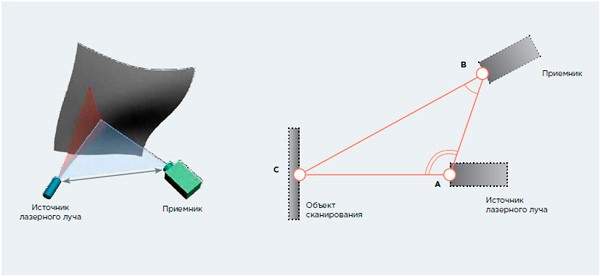
Фотограмметрия
Фотограмметрия это научно-техническая дисциплина, занимающаяся определением характеристик объектов, таких как форма, размеры, положение в пространстве и т.д., по их изображениям. Фотограмметрия использует все существующие виды изображений, полученные с помощью фотокамер, цифровых камер, телевизионных камер, сканерных съемочных систем, радиолокационных и лазерных съемочных систем и т.д.

Фотограмметрия развивается по трем основным направлениям. Первое направление связано с созданием карт и планов по снимкам. Это направление часто называют фототопографией. Второе направление связано с применением фотограмметрии для решения прикладных задач в различных областях науки и техники: в архитектуре, строительстве, медицине, криминалистике, автомобилестроении, робототехнике, военном деле, геологии и т.д. Это направление в фотограмметрии называют наземной или прикладной фотограмметрией. Третье направление – это космическая фотограмметрия. Снимки Земли, полученные из космоса, используются для изучения ее природных ресурсов и для контроля за охраной окружающей среды. Снимки других небесных тел, в частности Луны, Венеры, Марса, позволяют изучить их рельеф и получить много другой полезной информации.
Такое широкое применение фотограмметрии обусловлено следующими ее достоинствами:
- Высокая точность, потому что снимки объектов получают прецизионными камерами, а обработку снимков выполняют строгими методами.
- Высокая производительность, достигаемая благодаря тому, что измеряют не сами объекты, а их изображения. Это позволяет автоматизировать процессы измерений по снимкам и последующую обработку на компьютере.
- Объективность и достоверность информации, за счет того, что информация об объекте получается фотографическим путем.
- Возможность повторения измерений в случае получения спорных результатов.
- Возможность получения в короткий срок информации о состоянии, как всего объекта, так и отдельных его частей.
Раскрой материалов
Лазерная резка\гравировка
Лазерная резка — технология резки и раскроя материалов, использующая лазер высокой мощности и обычно применяемая на промышленных производственных линиях. Сфокусированный лазерный луч, обычно управляемый компьютером, обеспечивает высокую концентрацию энергии и позволяет разрезать практически любые материалы независимо от их теплофизических свойств. В процессе резки, под воздействием лазерного луча материал разрезаемого участка плавится, возгорается, испаряется или выдувается струей газа. При этом можно получить узкие резы с минимальной зоной термического влияния. Лазерная резка отличается отсутствием механического воздействия на обрабатываемый материал, возникают минимальные деформации, как временные в процессе резки, так и остаточные после полного остывания. Вследствие этого лазерную резку, даже легкодеформируемых и нежестких заготовок и деталей, можно осуществлять с высокой степенью точности. Благодаря большой мощности лазерного излучения обеспечивается высокая производительность процесса в сочетании с высоким качеством поверхностей реза. Легкое и сравнительно простое управление лазерным излучением позволяет осуществлять лазерную резку по сложному контуру плоских и объемных деталей и заготовок с высокой степенью автоматизации процесса.
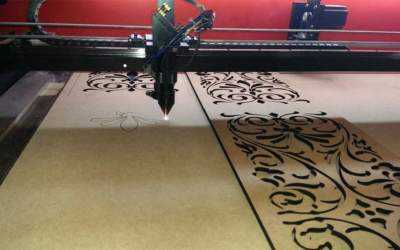
Лазерная резка осуществляется путём сквозного прожига листовых металлов лучом лазера. Такая технология имеет ряд очевидных преимуществ перед многими другими способами раскроя:
- Отсутствие механического контакта позволяет обрабатывать хрупкие и легко деформирующиеся материалы;
- Обработке поддаются материалы из твёрдых сплавов;
- Возможна высокоскоростная резка тонколистовой стали;
- При выпуске небольших партий продукции целесообразнее провести лазерный раскрой материала, чем изготавливать для этого дорогостоящие пресс-формы или формы для литья;
- Для автоматического раскроя материала достаточно подготовить файл рисунка в любой чертёжной программе и перенести файл на компьютер установки, которая выдержит погрешности в очень малых величинах.
Плоттерная резка
Режущим плоттером или каттером называют специальные приспособления для того, чтобы вырезать изображения из разных видов пленочных материалов. Режущий плоттер является распространенным инструментом в оформлении витрин, табличек на дверях офиса, при термопереносе на специальную одежду и еще некоторых областях. C помощью этого инструмента становится значительно проще производить шаблоны и для других сфер использования. Благодаря отличной отработанности, резка на плоттере становится возможным для частого использования, при этом нужно минимальное количество профилактических работ. Из этого следует, что такая технология является весьма экономичной. Цена на плоттерную резку зависит от сложности и количества работы. Из наиболее важных моментов использования режущих плоттеров можно отметить скорость резки, рабочую ширину и давление ножа.
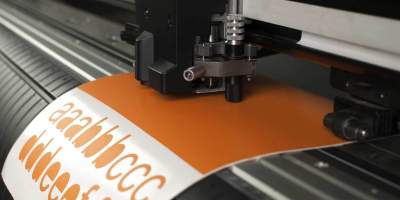
Технология плоттерной резки обычно производится по одной и той же схеме:
- Подготовить нужный рисунок в специальной векторной программе, к примеру, CorelDraw или же в любой другой, которая идет в дополнение к плоттеру. В то же время можно импортировать готовые векторные клип-арты.
- Заправить бумагу либо же край пленки в плоттер, опустить ролики, далее при использовании теста выставить необходимое давление ножа для прорезывания пленки, но чтобы при этом он не разрезал подложку, после чего выставить начальную позицию ножа, и отослать файл из компьютерной программы для резки.
- Когда плоттер закончит вырезать изображение, нужно убрать неиспользуемую пленку, а вырезанное изображение следует перенести на монтажку и далее на требуемую поверхность.